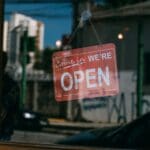
Retail Construction is a Difficult Business — But it Doesn’t Have to Be
Retail construction presents a number of significant challenges — here’s how innovative AEC technology can help.
The concept of the modern “chain store” traces its origins all the way back to 1859, when The Great Atlantic & Pacific Tea Company, perhaps better known as A&P, opened a handful of retail locations in New York City. The model proved effective, propelling the company down a path towards becoming the United States’ largest retailer for half a century (1915 to 1965).
Unsurprisingly, many other companies took note of A&P’s massive success and followed in its footsteps, updating and improving the model along the way in accordance with consumer expectations and preferences. And though the experience of walking into a sleek, ultra-modern Apple store might make the A&P model seem irrelevant, the underlying concept driving retail chain design today is exactly the same as it was 158 years ago: consumers crave consistency.
This is especially true when a company’s value proposition includes a specific lifestyle or set of values. When Howard Schultz returned from his “legendary” 1983 trip to Milan, he transformed Starbucks, what was still a small Seattle-only chain, into a bonafide cultural movement. Crucially, he recognized that in order to garner widespread loyalty, he needed to ensure his customers could depend on a consistent brand experience — whether they were ordering a latte in downtown Manhattan or a small town in rural Kansas.
The Many Challenges of Retail Construction
So, we’ve established that a consistent brand experience is important in a retail context. The problem is, from a construction perspective, this is an incredibly difficult thing to accomplish. Retail construction is a maze of rules and regulations relating to accessibility, environmental impact, equipment safety, layout constraints, not to mention resource limitations and landlord-related issues. In particular, the latter represents a serious roadblock to success.
I was recently involved in an informal evaluation of approximately 100 projects, of which, we determined, over 90% experienced a negative landlord impact (some very minor, some significant). Several deals even ended in financial and/or legal negotiations. These issues typically stem from logistical breakdowns and/or landlords not making good on their promises related to scope or scheduling.
Moreover, the construction process itself is inherently inconsistent. Some sites will be built from the ground-up, while others will be interior fit-outs (installed within existing structures). Each location will have its own unique characteristics, building layouts, neighborhood and/or environmental considerations, safety features — the list goes on and on. Deploying remote field teams across hundreds or even thousands of different sites creates enormous challenges related to efficiency and oversight.
Furthermore, as the building process becomes more complex, traditional methods of project coordination, reporting, and collaboration have become increasingly ineffective. This, of course, can lead to issues surrounding project efficiency, costly delays, and missed deadlines. When new locations don’t open on time, there’s an immediate and significant impact in terms of lost sales revenue, market share depletion, and wasted capital. And, one can imagine what that does to morale for a company or in the retail sector, in general.
For example, if the average big box retailer like Target is approximately 135,000 square feet, and the average annual cost of leasing commercial real estate in Philadelphia (which I consider my hometown) is roughly $19.99 per square foot, that boils down to about $225,000 per month — just to lease the space! If an opening is delayed six to eight weeks, that’s not an insignificant loss, even for a company the size of Target.
Tech-Forward Solutions
In order to stay a step ahead of the competition, retailers need to find a way to anticipate problems before they arise in order to avoid costly store development delays. Many are beginning to turn to innovative AEC technologies like building information modeling (BIM) to help address some of these longstanding issues with retail projects.
As a casual golfer, I have many putts that are far from the hole. I would love it if I was given a drawing that showed the line of the putt — a sketch, for example, indicating that I should aim six inches to the left of the hole to account for the slope in the green, and take back my putter 27.5 inches to account for the morning dew on the grass, which will slow the ball. Having that technology might not mean I’ll make 100% of my putts, but it would certainly increase my chances for success. That’s what BIM is: an accurate representation of what you’re getting into before you start.
BIM in Action
BIM isn’t exactly new, but recent developments in related areas — such as virtual reality, cloud computing, and laser scanning — have made it more practical and impactful to employ in the field than ever before.
Imagine you’re fitting out a new location in a historic, 85-year-old building — as I’m doing now in Ardmore, PA. This tends to present a number of problems from a construction perspective: uneven floors, crooked walls, deck beams at different heights, etc. Rather than rely on the original 2D plans from the landlord, which by now are most certainly inaccurate, you could use a 3D laser scanner to capture an incredibly detailed digital model of the space. This 3D model would allow you to test layouts, make material and labor cost estimations, and increase the accuracy of timeline projections.
In retail construction, projects are typically spread out across the country, making it difficult for design firms and other key stakeholders to visit each location in order to monitor project progress and provide real-time guidance. Virtual collaboration solutions, like virtual tours, allow design, engineering, and construction teams and owners to view and discuss the job together without having to travel to the actual site. This has been extremely helpful on projects I’ve been working on, given that the client’s Store Development team is located on the opposite side of the country, 2,900 miles away from the site.
Using reality capture technologies to remotely monitor projects not only gives you a clear window into the existing conditions in a given space — it also provides an incredibly accurate square footage reading, which, considering landlords’ tendency to overestimate the size of their properties, definitely comes in handy from a cost-savings perspective.
Tangible Returns
While these kinds of solutions do represent an additional investment upfront, most experts agree that it more than pays for itself — especially in complex, multi-location projects for institutional owners. As Dennis Shelden, co-founder of Gehry Technologies and Associate Professor at MIT Architecture, points out, “The general consensus is that 30% of all construction is waste.” He explains that by doing even just some of the simplest tasks with BIM, “you can save 10% of the building cost.” Essentially, by implementing BIM on any project, things will go smoother and cost less money. What does that do for company morale?
A McGraw-Hill Construction SmartMarket Report found that 86% of AEC firms that adopted a BIM tool saw improvements in design visualization and presentation; 85% were able to preemptively identify and resolve design conflicts; 82% reported reductions in downstream rework instances; and 81% saw fewer errors and omissions in construction documents. Together, these benefits resulted in significant project timeline reductions for 69% of the firms that were surveyed.
We’ve certainly come a long way since the first A&P market opened its doors more than a century and a half ago — shouldn’t the way we approach retail design and construction reflect that?
This article was originally published on LinkedIn Pulse.