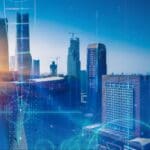
Pros and Cons of Prefabrication and Modularization Techniques
Throughout history, the construction industry has been characterized as a labor-intensive industry that is timely, costly, and produces excess waste at the expense of the environment. Over the past 100 years, contractors have used prefabrication and modularization techniques to reduce costs, enable process standardization, shorten lead times, improve construction quality, and reduce waste. Prefabrication is the process of assembling building systems to a nearly-complete state offsite to later deliver to the project site for installation. Modularization involves constructing a finished project offsite and then delivering it to the construction site to assemble with other modules to create the final product.
According to McGraw Hill Construction’s 2011 report, “Prefabrication and Modularization: Increasing Productivity in the Construction Industry,” modern technology has allowed these techniques to overcome the stigma of cheapness and poor quality, thereby driving industry productivity. Approximately 85% of respondents to McGraw’s survey use these strategies to design and construct projects at some level.
Pros of Prefabrication and Modularization
The primary advantage of these techniques is increased productivity, especially when construction schedules are tight, bids are competitive, and skilled labor is scarce. Other advantages include enhanced simplified onsite logistics, less risk of theft and vandalism, and better protection from weather damage. Prefabrication and modularization help decrease material waste and create less disruption to the surrounding environment. Lean approaches can help construction companies achieve green project goals and eliminate environmental waste in the design phase. Modular buildings are also useful and cost-effective for temporary and seasonal work structures
Cons of Prefabrication and Modularization
There is a common misconception that modular and prefab buildings are not built using the same level of quality as traditional site-built buildings and therefore, cannot adhere to architectural specifications. Ongoing education in the construction industry is necessary to propel the evolving market forward. Modular Today points out that commercial modular buildings often have limited customization and service areas. Building designs have limits on dramatic aesthetic changes, and costs increase greatly when building sites are located more than 500 miles from the factory.
Trends of Prefabrication and Modularization
Some markets have taken advantage of prefabrication and modularization techniques more than others. And according to FMI Corporation’s “Prefabrication and Modularization in Construction 2013 Survey Results”, the markets for healthcare, education, and lodging are expected to grow faster in the years ahead. Most prominently in the healthcare industry, growth depends on these techniques’ adaptability in complex buildings, the economic climate in the country, and the ability to expand and be replicated over time.
To expand the use of prefabrication and modularization in projects, construction professionals should calculate their return on investment and measure the expected pay-back time frame. Other considerations include delivery times, quality control, procurement, and labor relations. These industry techniques are not new, but they are changing as the needs of society evolve and become more specific and sophisticated.
Photo credit: seier+seier, jessica.dailey via Flickr